Ink and Fluid Development
ImageXpert Partners
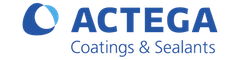
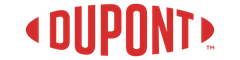
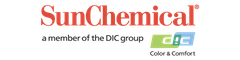

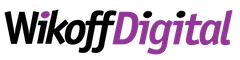
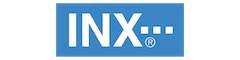
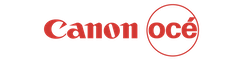
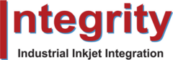
ImageXpert has roots in the inkjet printing industry that go back over 25 years. The earliest ImageXpert systems for measuring print quality were used by the founding companies of inkjet technology. At that time, inkjet printers were primarily used for printing on paper and were produced by only a handful of well-known companies such as HP, Epson, Canon, Brother, and the like. Today, inkjet printing has infiltrated almost every manufacturing sector: from printing on textiles, to packaging, to printed electronics, to glass, and more. This wide range of applications calls for a wide range of inkjet inks, each with their own unique base materials, colors, additives, and properties. Today, there are several thousand companies focused on inkjet ink development, with more being added every day.
Common Challenge: More Complex Applications
In the past, inkjet technology was more rudimentary, and you could eventually produce a usable ink by running different samples through a printer until you found a winner. Today, the requirements for what makes an ink usable have been raised because printers are going faster, with more complex fluids, on more challenging substrates. Now, you’ll need precise control over drop volume, drop velocity, number of satellites, and sustainability over time in order to have a competitive product. The JetXpert Dropwatcher has been widely adopted for inkjet ink development because it allows researchers to learn more about their ink and optimize its formulation faster than ever before.
Critical Measurement: Print Quality
In many cases where the ink will be used on an extremely absorbent substrate (such as textile) or an extremely unabsorbent substrate (such as plastic), an intermediate fluid is used to prime and prepare the surface. Another element of providing a complete solution to the customer is knowing what pretreatments and coatings work well with a particular ink formulation, and studying print quality systematically can help match an ink and pretreatment faster and more effectively.
Learn How Evonik Industries Mastered Producing Additives for InkjetCommon Challenge: Changing Industry
As new applications are introduced to the industry, often this results in new printheads being developed to meet them. What this means for inkjet ink development is that there is always new R&D to be done – whether it is developing fluids for a new printhead, or developing fluids for a new application. Because projects are always changing, inkjet developers turn to the modular JetXpert Print Station, an all-in-one dropwatcher and sample printer compatible with every printhead on the market. Rather than collecting a museum of expensive printers, they simply swap out the printhead on the JetXpert Print Station to match their current project. Retrofitting a JetXpert system is one of the fastest and lowest cost ways to evaluate a new printhead or application and stay nimble in a changing industry.
Critical Measurement: Waveform Optimization
When inkjet applications were more forgiving, a standard, off-the-shelf waveform was sufficient for nearly every ink. Today, the stricter demands of the industry require that waveforms be optimized to each particular fluid, so that they produce the fastest, cleanest, most consistent drops possible. It is a huge advantage for ink developers to be able to provide a complete solution to their customer, including a waveform tailored to their specific ink and needs.
Read “How to Optimize a Waveform”Common Challenge: Jetting Failure
Regardless of the application, all ink and fluid developers face similar challenges with the behavior of their ink. Common failures like wetting of the nozzle plate, satellite formation, or issues with open time / latency are hard to understand and correct without experience. To help, we’ve put together a series of articles that explain what could be causing these behaviors, as well as offer ideas on how to fix them:
What Causes Wetting?
How to Stop Satellites From Ruining Your Print
The Top 4 Solutions for Latency / De-Cap
Recommended Products for Inkjet Ink Development
- XSweep
- Frequency Sweep
- Wetting Camera
- PrintXaminer
- JetXpert Print Station
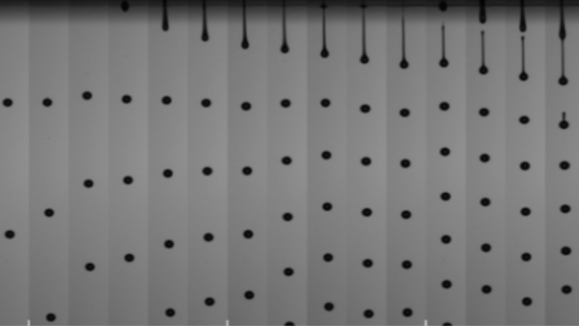
XSweep
Make the process of waveform optimization more automated with XSweep. Simply specify which waveform parameter you want to adjust, like voltage or pulse width, and enter a range of values to test, and the software will automatically capture images and data for each one.
Learn More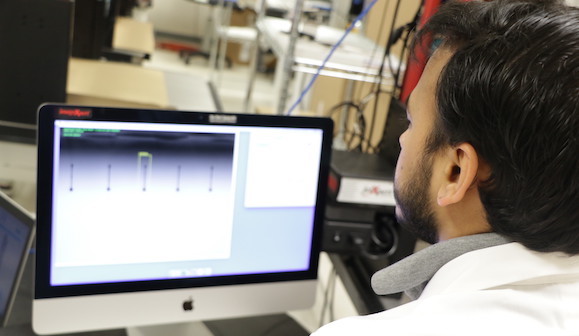
Frequency Sweep
Automatically ensure that your jetting is consistent at any printing speed. Frequency Sweep lets you enter a list of firing frequencies to test, and the software will automatically collect images and data for each one.
Learn More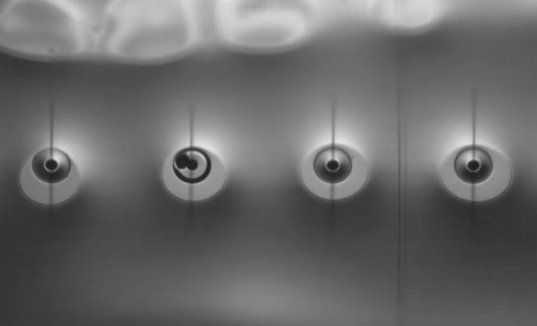
Wetting Camera
Add a second camera to your JetXpert to visualize the nozzle plate and monitor ink buildup. Simultaneously view the drops and the nozzles to understand the causes and performance impact of wetting, debris, or damage on the nozzle plate.
Learn More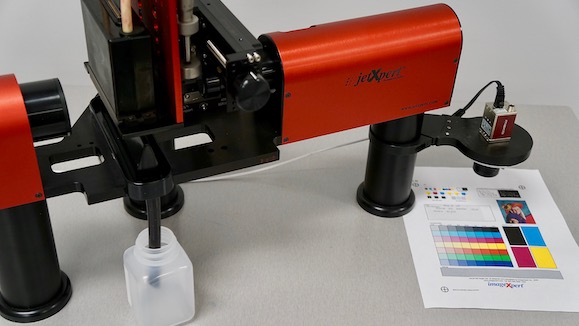
PrintXaminer
Just as it is critical to study the drops in flight, it is also important to study the drops once they have hit the substrate. The PrintXaminer is designed to bring seamless print quality measurement capabilities to your dropwatching and printing system. The system is ready to use on day one with a pre-configured test target and measurements for line quality, dot size, bleed, inter-color bleed, and more.
Learn More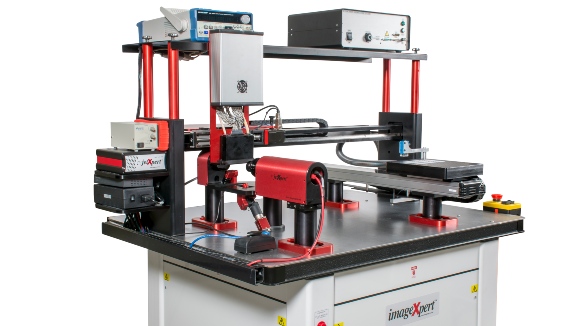
JetXpert Print Station
All-in-one dropwatching, sample printing, and print quality analysis for more efficient testing
Learn MoreWhether you are looking for a quote, demo, or would like more information on a system for inkjet ink development, we’d love to hear from you.