Additive Manufacturing
ImageXpert Partners
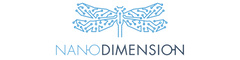
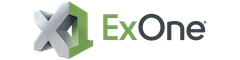
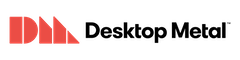
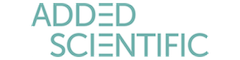
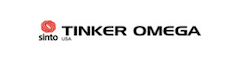
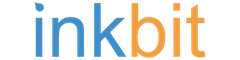
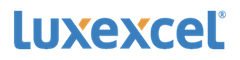
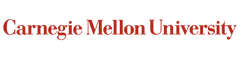
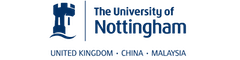
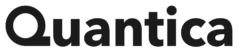
Over the past decade, we’ve seen many large manufacturers taking a growing interest in additive manufacturing, also known as 3D printing, using a technique called Binder Jetting. In this process, inkjet printheads apply a glue-like fluid onto a bed of powder. A new layer of powder is reapplied, and the process is repeated, building up the part one layer at a time.
Several aspects of inkjet technology make it well-suited for 3D printing applications:
- Industrial inkjet is a well-established technology with a wide variety of printheads and fluids to choose from, giving developers the option to 3D print using an aqueous, solvent, or UV-curable binder.
- Additive manufacturing requires a high level of precision in the placement of the binder fluid, and inkjet offers micron-scale placement of drops anywhere from 1 pL to 250pL in volume.
- Inkjet is a relatively fast and inexpensive process that can easily be scaled to produce parts of a variety of sizes.
- Many raw materials can be produced in a powder form, so parts can be produced in a wide variety of metals, sand, ceramics, and composites.
Common Challenge: Printhead Selection
The resolution and drop size of the printhead is an especially important factor for 3D printing, as it is less forgiving than other applications. Applications like textiles, packaging, and graphics will still produce a usable product across a wide range of print resolutions, but a part 3D printed with inkjet will only work if the resolution and drop size is just right. Drops that are too large will produce parts that are less precise, distort due to saturation, and take too long to dry. Drops that are too small are more difficult to control, require more layers to produce a part, and might not saturate the surface of the powder and form a proper bond. A good place to start is by examining the size distribution of your powder and making sure it is a match with the drop size and resolution of your printhead.
Critical Measurement: Drop Volume
Don’t assume that the drop volume you are jetting matches the one in the printhead specs; other factors such as the properties of the fluid, the waveform, and the temperature of the fluid can cause the size of the drops to vary by up to 400%. The correct drop volume is the difference between a failed part and a successful build, so our customers use the JetXpert Dropwatcher to measure and optimize drop volumes for their application.
Learn MoreCommon Challenge: Material Compatibility
The fluids used in binder jetting contain binder materials, which means that keeping the printhead from gluing itself shut is a unique challenge to be addressed. Minimizing missing jets is especially critical to additive manufacturing because they can impact the structural integrity of the part. Other applications can rely on software tricks and nozzle compensation to accommodate small defects, but in additive manufacturing all the nozzles need to work all the time. To combat this, we’ve seen that most of our customers in the 3D printing industry are experimenting with recirculating inkjet printheads, as this technology is well-established in other industries where fluid drying or clogging is common. Along with recirculation, developers rely on printhead spitting and tickle pulses to help maximize the open time of the printhead.
Critical Measurement: Drop Speed
If the drops are traveling too slow, they won’t fully penetrate the surface of the powder; if the drops are traveling too fast, it can cause a phenomenon referred to as “powder splash”, where the drops hit with such force that it causes powder to go airborne. As this powder collects on the nozzle plate and accumulates, it will eventually cause nozzles to fail. You can customize your JetXpert Dropwatcher with the Surface Add-On to study the size and speed of drops and how they influence the reaction with the powder by watching the process live.
Learn MoreRecommended Products for Additive Manufacturing
- JetXpert Drop Analysis
- JetXpert Surface Add-On
- Linear Stage Print Station
- Ink Supply
- Printheads
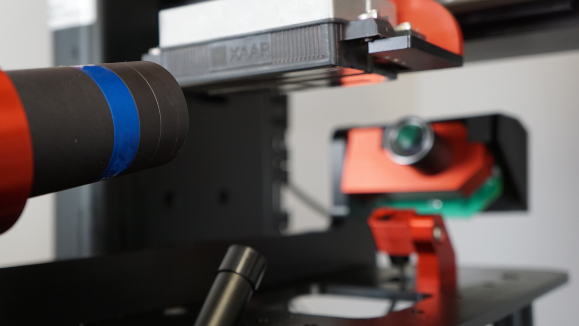
JetXpert Drop Analysis
Perfect your jetting or dispensing with industry-leading drop visualization and measurements.
Learn More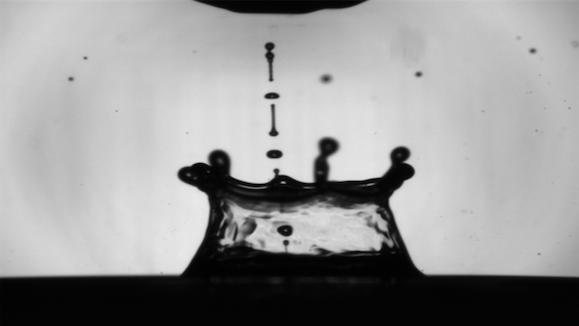
JetXpert Surface Add-On
See drops hitting the substrate with your JetXpert system to study splashing, spreading, powder movement, and more. This is not your father’s contact angle measurement tool – these are actual-size, jetted drops in a printing environment.
Learn More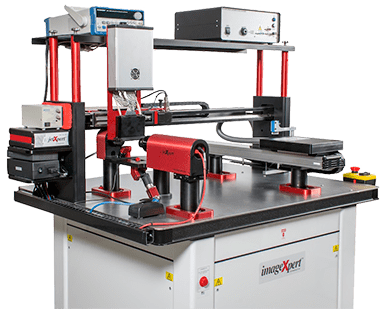
Linear Stage Print Station
All-in-one dropwatching, industrial multipass printing, and print quality analysis for more efficient testing.
Learn More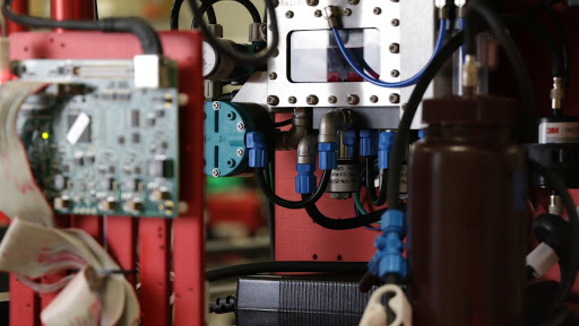
Ink Supply
Easy to use inkjet ink supply systems, whether you are looking for production-level results or simplicity for the lab
Learn More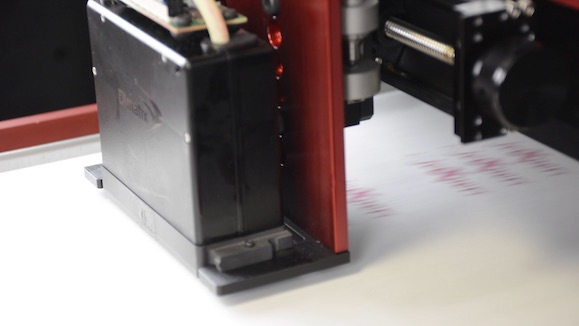
Printheads
The JetXpert system is compatible with industrial inkjet printheads from all major manufacturers including: Epson, Fujifilm Dimatix, HP, Kyocera, Ricoh, Seiko, Toshiba Tech, Xaar, and Xerox
Learn MoreWhether you are looking for a quote, demo, or would like more information on a system for additive manufacturing, we’d love to hear from you.