How to Stop Satellites From Ruining Your Print
Last Updated on June 25, 2024 by ImageXpert Team
In this post, we have a look at one of the most common inkjet problems seen by our customers: satellite drops. Satellites, the small droplets unintentionally formed during jetting, can cause major print quality and system maintenance headaches. We will discover that there are multiple potential causes of satellites and explore some of the ways to minimize their formation and effect. This post was produced with knowledge and data contributed by System Ceramics, a leader in the inkjet ceramics market.
TELLTALE SIGNS
One easy way that you might be able identify the presence of satellite drops and mist (exceptionally small satellites) is by looking at your printer itself. If you open up the printer and the inside is a nice shade of CMYK, then you have determined that you have satellites. By studying the color, you might even be able to identify if a particular ink has worse satellite problems than the others.
If you happen to have a JetXpert dropwatcher already, you might be able to see satellites in the jetting itself. We have labelled some of the parts of the image to introduce some terminology that we’ll use throughout this article.
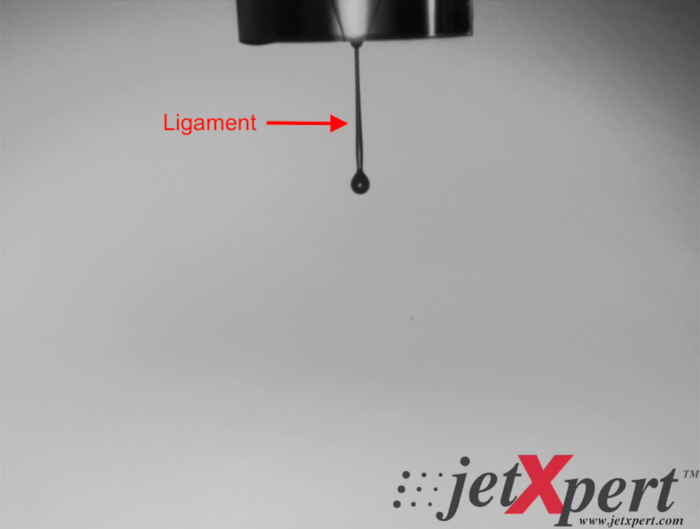
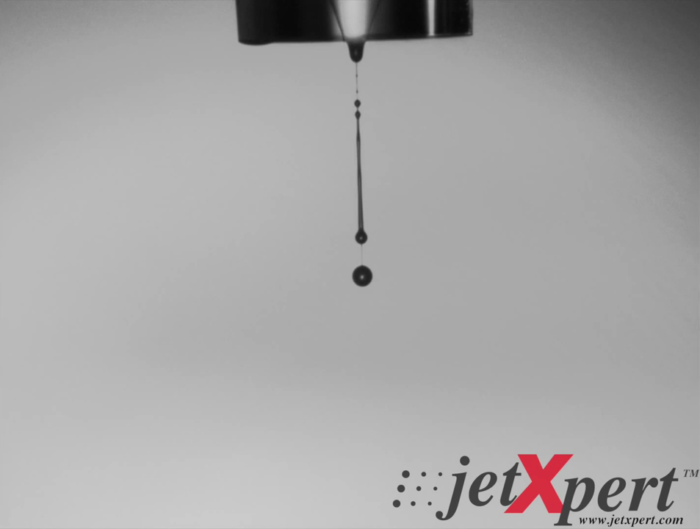
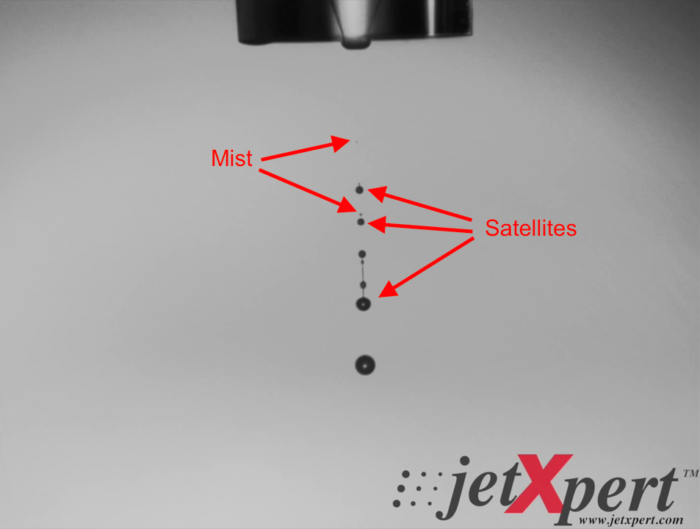
Satellites also show up in the printed substrate. In multiple-pass printers, such as those used in graphics, satellite drops are most often seen as an “overspray” effect at the ends of the carriage where the airflow is dominated by the entrained flow under the carriage. In the middle of the carriage, satellite drops can often be seen surrounding print detail like text.
If the carriage speed is higher or the print gap is larger, then the effects tend to be worse. This is for two reasons: (1) the turbulence from airflow interactions can increase significantly and (2) the stray satellite drops have more distance over which to decelerate and thus become misdirected.
WHAT CAUSES SATELLITES?
The process of forming inkjet drops essentially involves squeezing a low viscosity fluid through a tiny hole, which can subject the fluid to quite a lot of forces. The harder the ink is pushed, the more stress on the fluid, and the more formulation details, like viscosity, surface tension and particle content, impact the drop formation behavior.
An interesting finding is that the number of satellites formed is often proportional to the ligament length, which in turn is also proportional to several measurable characteristics of your system. System Ceramics presents the formula for ligament length as follows:
As you can see, some of these aspects of the system are for the most part fixed (e.g. nozzle diameter, density) whereas some of them you have control over. Keep this in mind as we look at potential solutions for the satellite problem.
IMPACT OF WAVEFORM
Because satellites are formed by forces on the fluid, and the waveform provides the driving force behind jetting, investigating the design of your waveform seems like a logical place to begin. Let’s make a real comparison of what happens as a print head is driven to higher and higher drop velocity by increasing the amplitude of the waveform. The first image (created using JetXpert Stitch) is the drop formation at 16V waveform amplitude, the second is that same drop formation at 20V. Remember from our formula above that ligament length (and number of satellites) is directly proportional to drop velocity. The practical results show the same thing: at higher voltages the ligament is longer, the drop is traveling faster, and there are more satellites.
Based on this, an easy way to decrease the formation of satellites is to decrease the amplitude of the waveform pulses, lessening the force on the fluid. However, this also might decrease the drop volume and velocity, the impact of which needs to be carefully considered. Whether or not this is an acceptable compromise is completely dependent on your particular system and application. For more information about optimizing waveforms for drop volume, velocity, and satellite formation, check out our dedicated post on Waveform Optimization.
Join Our Mailing List
IMPACT OF INK FORMULATION
If waveform optimization is not enough to eliminate satellites, modifying the ink itself is another option. The study of fluids under stress and shear is called rheology, and the inkjet process is so extreme that it has driven a lot of study into inventing techniques that can try and predict things like satellite drops. A lot of research groups have studied model systems and real fluids and come up with some helpful rules, based on so-called dimensionless variables (like Weber number, or Ohnesorge number). The issue is that a lot of different fluid measurement are required to be able to calculate these quantities, which might not be for everyone. Here we try to simplify things down to two important variables: viscosity and surface tension.
Viscosity is always going to be an important variable in inkjet because it defines how easily the inks will flow through the head channels and squeeze out of the nozzle. In this case, it also influences how the ligament might extend before pinching off or breaking up. Based on our formula above, a lower viscosity should produce shorter ligaments and fewer satellites. Practical experimentation also suggests the same. System Ceramics performed a test where the viscosity was lowered for otherwise identical fluids, producing drops that had shorter ligaments without loss in velocity.
With this in mind, if you can lower the viscosity of your fluid, then you may see a reduction in satellites. It is important to remember though that in most cases, the viscosity of the ink is confined to a range that the head manufacturer stipulates. You may be limited in your fine-tuning for this reason.
Surface tension also has a lot to say about how a longer ligament will break up since it determines how much the ink would like to form a nice round drop again. Theory suggests that higher surface tension will decrease the ligament length and number of satellites. However, this is not so easy in practice because you have to have precise control over the surface tension of the drop at the moment that it is being formed. It is more challenging to adjust the surface tension at 50-100 us after being jetted than at 10 seconds.
Finally, for many types of inks we have to consider the particle content, which for a pigment-based ink can be a big factor. We can see this by comparing the two images below showing white (left) and black (right) prints from the same printer, deposited in the same resolution (although different substrates). The white clearly show more satellite drops, which is not untypical because of the typically much higher solid content of larger primary particle size.
PRINTER DESIGN
Apart from the waveform, which is related to the drop velocity as mentioned above, other aspects of the machine design can influence the impact of satellites significantly. While the machine design might not be able to prevent the satellites from being formed, it certainly can play a role in containing them.
One way to control satellites is by controlling the effect of electrical charge. Since many inks are insulating, the printhead can induce a small charge onto the droplets and that can have surprisingly strong effects on the printing, especially if the substrate is also non-conducting. This is not a new issue as the patent image below, showing an electrostatic mist removal concept from HP confirms.
The usual way of mitigating these effects is to ensure printer components are well grounded and that ionization bars are used to control the build-up of static electricity when the substrate is insulating. There are no hard-and fast rules, but it is important to consider as static charge is often one of the reasons it is harder to connect a dropwatcher result to a printer failure.
As a simpler measure, many different printer manufacturers have patented air inlet, air extraction, and filtration devices to collect the ink before it reaches the substrate. When UV curing ink, this also prevents the ink from collecting on the UV cure lamps where it can eventually block the curing process. The picture below comes from such a patent.
MEASURING YOUR PROGRESS
It’s easy to see satellites visually using the JetXpert dropwatcher, but it is also important to determine if those satellites actually have an effect by studying the print. Some applications are more forgiving for satellites than others, depending on the absorbency of the substrate, throw distance, and viewing distance. For this reason, it is difficult to determine if the amount of satellites is acceptable based on the dropwatching alone.
Analyzing the printed image will give you more insight into how the jetting quality relates to the end product quality. This can be done automatically using the same machine vision technology the JetXpert is built on. For example, you can easily view satellites with the dropwatcher, print a sample image, and automatically count the number of satellites present in the print all on one machine. For more information about these systems, such as the one shown below, check out our Print Station page or contact ImageXpert.