印刷品質を損なうサテライト滴を無くすには?
Last Updated on 6月 25, 2024 by ImageXpert Team
今回の記事では、お客様の間で最もよく見られるインクジェットのトラブルの一つである「サテライト滴」についてご紹介します。サテライトとは、インクの吐出に伴い意図せず形成された小さな液滴のことで、印刷品質やシステムメンテナンスの面で大きな問題となります。この記事では、サテライトが発生する複数の原因を紹介し、サテライトの発生と影響を最小限に抑えるための方法をご紹介します。この記事は、インクジェットセラミックス市場のリーダーであるSystem Ceramics社が提供する知識とデータをもとに作成されました。 System Ceramics, a leader in the inkjet ceramics market.
状況証拠
サテライト滴やミスト(非常に小さなサテライト)の存在を簡単に確認する方法として、プリンター本体を見るという方法があります。プリンターを開けてみて、どこかしらにCMYKの色が着色していれば、それはサテライトやミストが付着したものです。また色ごとの付着量に着目すると、あるインクが他のインクよりもサテライトの問題を抱えているかどうかがわかるかもしれません。
JetXpert液滴観測装置を既にお持ちの方は、液滴飛翔観察画像そのものの中にサテライトを見ることができるかもしれません。この記事で使用する専門用語(リガメント、サテライト、ミスト)を紹介するために、画像の一部に説明を付けました。
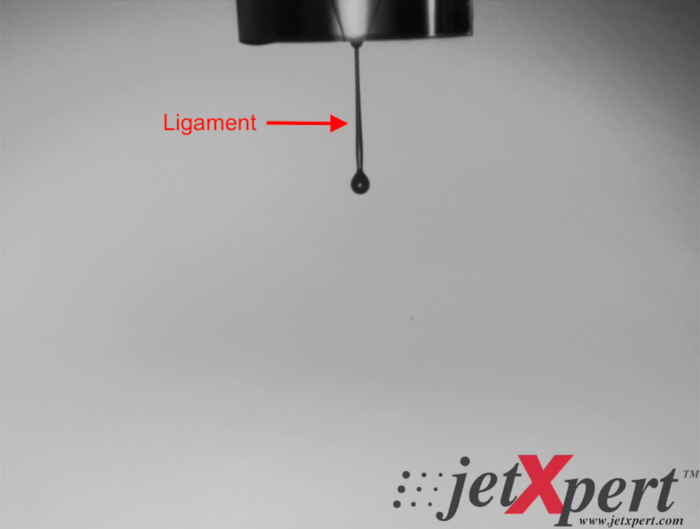
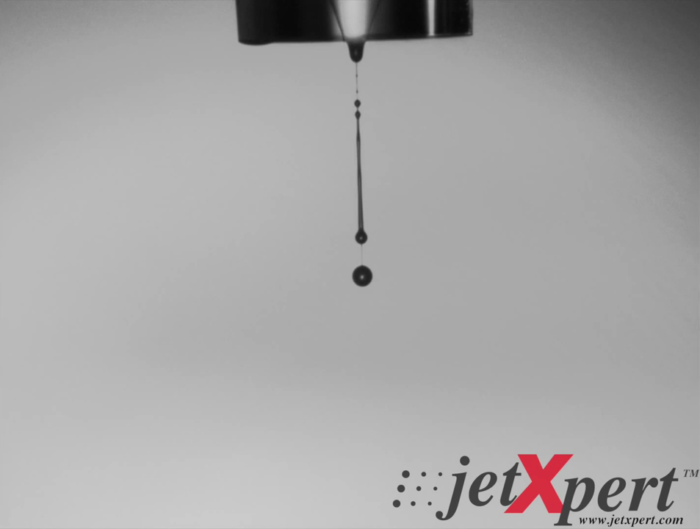
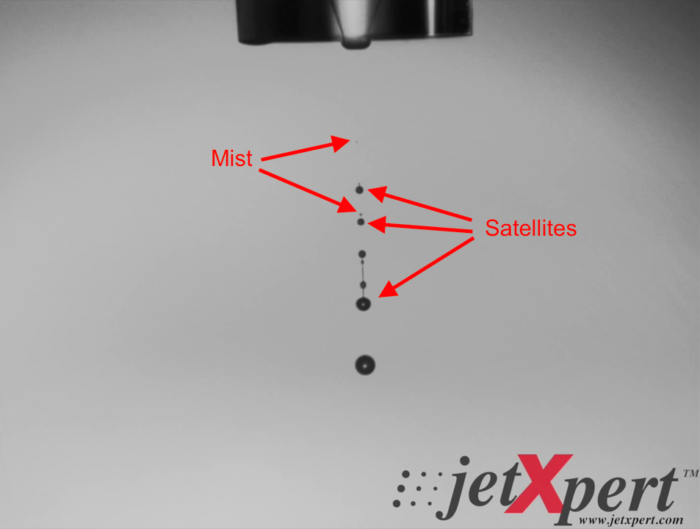
また、サテライトは印刷対象の表面にも現れます。グラフィックス用途向けなどのマルチパスプリンターでは、キャリッジ下の巻き込み気流が支配的ゆえ特にキャリッジの端部に位置するヘッドで、サテライト滴が「オーバースプレー」効果として見られることが多くあります。また、キャリッジの中央部では、文字などの印刷部分を囲むようにサテライト滴が見られることがよくあります。
キャリッジスピードが速かったり、ヘッドギャップ(紙面間距離)が大きかったりすると、効果が悪くなる傾向にあります。これには2つの理由があります。(1)気流の相互作用による乱れが大きくなること、(2)飛翔中のサテライト滴が減速する距離が長くなるため、着弾位置の誤差がより大きくなること。
サテライト滴の発生原因は?
インクジェットの液滴を形成するプロセスでは、基本的に、小さな穴から低粘度の液体を押し出すことで、液体にかなりの力が加わります。インクを強く押せば押すほど、流体にかかるストレスは大きくなり、粘度、表面張力、粒子の含有量など、処方の詳細が液滴形成の挙動に影響を与えます。
興味深いことに、形成されるサテライトの数はリガメントの長さに比例することが多く、その長さはシステムのいくつかの測定可能な特性にも比例します。System Ceramics社では、リガメント長の計算式を次のように示しています。
式を見てわかるように、ノズルの直径や密度など、システムの中でほとんど固定されているものもあれば、変更可能なものもあります。このことを念頭に置いて、サテライト滴の問題の解決策を考えていきましょう。
波形の影響
サテライトは流体にかかる力で形成され、インク吐出の原動力はヘッド駆動波形であることから、波形の設計から検討することは理にかなっていると言えます。では、波形の振幅を大きくして液滴速度をどんどん上げていくとどうなるか、実際に比較してみましょう。最初の画像(JetXpert Stitchで作成)は、波形の振幅が16Vのときのドロップ形成で、2番目の画像は同じドロップ形成を20Vでおこなったものです。リガメントの長さ(およびサテライトの数)がドロップの速度に正比例することを、上の式で思い出してください。実際の結果も同じで、高電圧ではリガメントが長くなり、液滴の移動速度が速くなり、サテライトの数も多くなります。 JetXpert Stitch) is the drop formation at 16V waveform amplitude, the second is that same drop formation at 20V. Remember from our formula above that ligament length (and number of satellites) is directly proportional to drop velocity. The practical results show the same thing: at higher voltages the ligament is longer, the drop is traveling faster, and there are more satellites.
このことから、サテライト滴の形成を減らすためには、波形パルスの振幅を小さくして流体にかかる力を小さくすることが簡単な方法です。しかし、この場合、液滴の体積や速度が低下する可能性があり、その影響を十分に考慮する必要があります。これが許容できる妥協点であるかどうかは、お客様のシステムやアプリケーションによって全く異なります。液滴体積、速度、サテライト形成に関連した波形の最適化については、専用の記事「波形の最適化」をご覧ください。 Waveform Optimization.
メーリングリストに登録
インク処方の影響
波形の最適化だけではサテライト滴を除去できない場合は、インク自体を変更するという方法があります。応力やせん断を受ける流体の研究はレオロジーと呼ばれていますが、インクジェットプロセスはその極端な題材のため、サテライト滴を予測する技術の開発に向けて多くの研究がおこなわれています。多くの研究グループがモデルシステムや実際の流体を研究し、いわゆる無次元変数(ウェーバー数やオーネゾルゲ数など)に基づいた有用なルールを導き出してきました。問題は、これらの量を計算できるようにするには、多くの異なる流体測定が必要であり、誰にでもできるというわけではありません。ここでは、粘度と表面張力という2つの重要な変数に絞って、物事を単純化してみます。
インクジェットにおいて、粘度は常に重要な変数です。なぜなら、インクがヘッドチャネルを流れ、ノズルから絞り出される際の容易さを規定するからです。また粘度は、リガメントがどのくらい伸びてから切れたり分解したりするかにも影響します。上記の計算式から、粘度が低いほどリガメントは短くなり、サテライトも少なくなるはずです。実際に実験してみても、同じことが言えます。System Ceramics社では、同じ流体で粘度を下げた実験をおこなったところ、速度を落とさずにリガメントを短くした液滴が得られました。
つまり、インクの粘度を下げることができれば、サテライトが減る可能性があるということです。ただし多くの場合、使用できるインクの粘度はヘッドメーカーが定めた範囲に限定されています。そのため、微調整には限界があるかもしれません。
表面張力は、長いリガメントがどのように分かれるかについても関係しています。理論的には、表面張力が高ければ、リガメントの長さやサテライトの数を減らすことができます。しかし、実際には、液滴が形成される瞬間の表面張力を正確にコントロールしなければならないので、そう簡単にはいきません。表面張力の調整は、10秒後よりも吐出後50〜100マイクロ秒の間振る舞いを制御することの方が難しいのです。
最後に、多くの種類のインクでは粒子の含有量を考慮しなければなりませんが、顔料ベースのインクでは大きな影響因子となります。下の2つの画像は、同じプリンタで同じ解像度で印刷した白(左)と黒(右)を比較したものです(印刷対象素材は異なりますが)。白には明らかに多くのサテライト滴が見られますが、これは一般的に一次粒子径が大きく固形分が多いことから、珍しいことではありません。
プリンターの設計
前述した液滴速度に関係する波形以外にも、プリンター設計そのものもサテライトの影響に大きく影響します。マシンの設計は、サテライトの形成を防ぐことはできないかもしれませんが、サテライトを封じ込める役割を果たすことはできます。
サテライトを制御する一つの方法は、電荷の影響をコントロールすることです。多くのインクは絶縁性であるため、プリントヘッドは液滴に小さな電荷を帯びさせる可能性があります。特に印刷対象素材が非導電性である場合には、印刷に驚くほど強い影響を与える可能性があります。この問題は、HP社の静電式ミスト除去のコンセプトを示す下記の特許画像が示すように、特に新しい問題ではありません。
これらの影響を軽減するための一般的な方法は、プリンタの部品が十分に接地されていることを確認し、印刷対象素材が絶縁されている場合には、静電気の蓄積を制御するためにバータイプのイオナイザーを使用することです。厳密なルールはありませんが、液滴観測装置の結果をプリンターの故障と結びつけるのが難しい理由の一つが静電気であることが多いので、考慮することが重要です。
よりシンプルな対策として、サテライトやミストが印刷対象に到達する前に回収するための空気吸入口、空気抽出口、濾過装置は、多くのプリンターメーカーが特許を取得しています。また、UV硬化インクの場合は、UV硬化ランプにインクが付着して硬化が阻害されるのを防ぐことができます。下の写真は、この特許から生まれたものです。
進捗状況の計測
JetXpertの液滴観測装置でサテライトを視覚的に確認するのは簡単ですが、そのサテライトが実際に影響を与えているかどうかをプリントを見て判断することも重要です。アプリケーションによっては、印刷対象素材の吸収性、紙面間距離、印刷物の視認距離などにより、サテライトに寛容なものもあります。そのため、液滴観測だけでサテライトの量が許容できるかどうかを判断するのは難しいのです。
印刷された画像を分析することで、インク吐出の品質と最終製品の品質がどのように関連しているかをより深く知ることができます。これは、JetXpertと同じマシンビジョン技術を使って自動的におこなうことができます。例えば、液滴観測装置でサテライトを見て、サンプル画像をプリントし、プリントに存在するサテライトの数を自動的にカウントするといったことが、1台のマシンで簡単にできるのです。このようなシステムの詳細については、JetXpertプリントステーションのページをご覧いただくか、ImageXpert社にお問い合わせください。 Print Station page or contact ImageXpert.