JetXpert Printers
Streamlined Inkjet Development
If you have a designated dropwatcher and a designated printer, switching back and forth between these two tests can be time-consuming. Changing inks, waveforms, substrates quickly on a production printer is no small feat. JetXpert printing systems incorporate everything you need for inkjet development on one platform, allowing you to move between tests with ease.
Modular Design
We know your R&D projects can change at a moments’ notice, so JetXpert printers are built for it. They are compatible with printheads and drive electronics from every major manufacturer, and you can easily swap between them in minutes.
View DriversPowerful Analysis Tools
We started with an open architecture, giving you full control over all aspects of the printing process. Then we added our industry-leading machine vision analysis systems to measure every stage of the printing process. Then we automated the testing and data capture – making a JetXpert printer the ultimate testing platform.
Products
- JetXpert Print Station
- JetXpert Print Station R2R
- JetXpert Print Lab
- JetXpert Print Pod
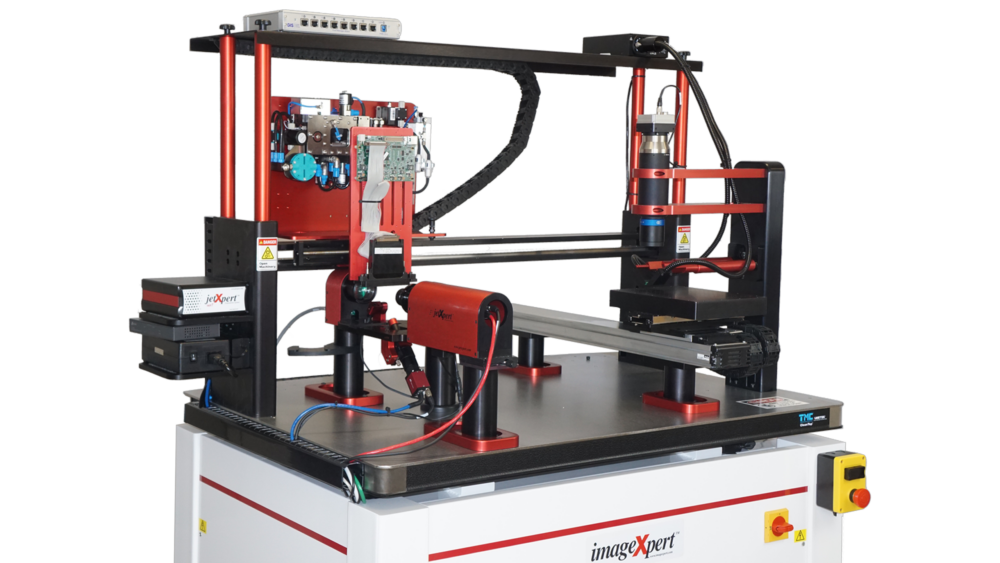
JetXpert Print Station
Achieving pilot production status has never been easier. Print with production quality and speed, with unmatched design flexibility
Learn More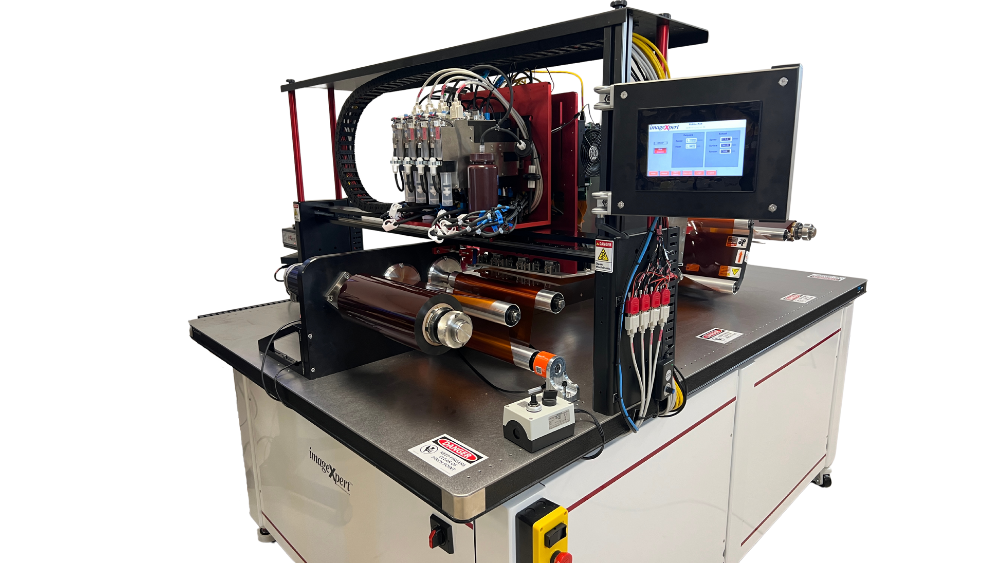
JetXpert Print Station R2R
Achieving pilot production status has never been easier. Continuously print with production quality and speed, with unmatched design flexibility
Learn More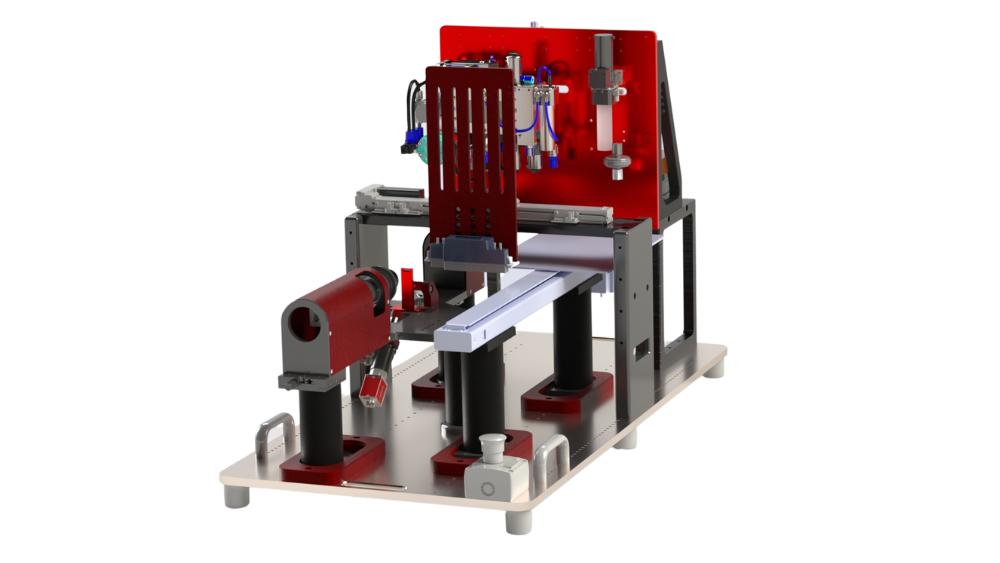
JetXpert Print Lab
Customizable inkjet analysis and printing platform in an lab-friendly package
Learn More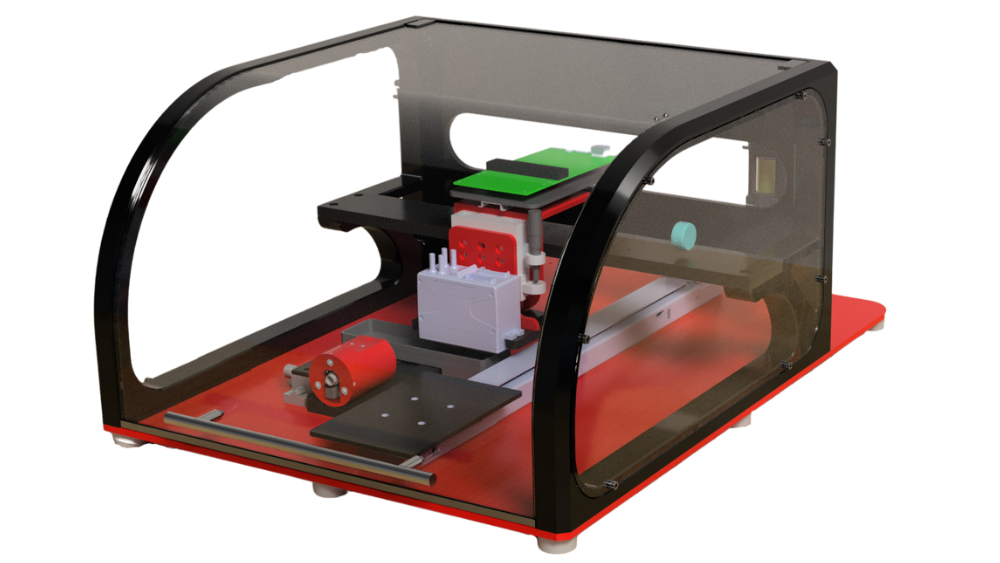
JetXpert Print Pod
Get started with dropwatching and sample printing in a compact desktop format
Learn MoreNot Sure Where to Start? Let Our Team Guide You
The Role of JetXpert Printers in Industrial Inkjet Printing
The idea for the JetXpert Print Station came directly from our customers. For years they had been relying on off-the-shelf printers for their day-to-day inkjet development and were frustrated by the inefficiency of it. Industrial printers are robust machines and not built to be easily reconfigured, so tasks like changing inks, printheads, and waveforms took hours and hours. The machines were large, requiring an entire industrial printing lab just to accommodate the equipment for a few different printheads or substrates. And if they wanted to evaluate a new printhead, it would require buying a brand new printer, taking up more time, money, and space.
Worst of all, the JetXpert Dropwatcher had become an essential part of their inkjet development, and it was completely isolated from these printers. After performing testing on the dropwatcher, the researchers would have to mimic the setup on another machine before being able to see how the settings performed in actual industrial printing situations. They were wasting time having to do everything twice and reached out to us for help. Soon, the JetXpert Print Station was born.
The JetXpert Print Station is designed to replicate the most essential parts of industrial inkjet printing, without all of the complication. We’ve kept the main components like substrate transport and ink curing, and stripped everything else out, leaving you with a flexible, easy-to-use machine. Because it is so simple, it is easy to make modifications to the system over time, like testing different printhead models, different substrates, or different printing conditions. One system is adaptable to grow with you over time as your needs change.
The efficiency of development on a JetXpert Print Station is unrivaled. The printhead, drive electronics, and ink supply are used for both dropwatching or printing, moving between the two tests with ease. By using the same exact equipment for both tasks, you can move quickly yet know for certain that the testing conditions are identical. In minutes, you can measure the velocity of drops produced with a certain waveform, print samples on different substrates, and study the impact of each combination on the print quality. The faster you can move between dropwatching and printing, the faster you can understand how a change to one impacts the other.
Let’s Talk
Whether you are looking for pricing, a demo, or training on a JetXpert industrial printing system, we’d love to hear from you.